Evolusjon av industrielt vedlikehold fra opprinnelse til i dag
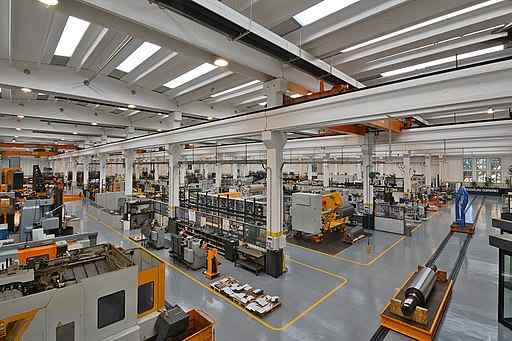
- 2887
- 418
- Magnus Sander Berntsen
De Industriell vedlikeholdsutvikling Det begynte å være mer viktig etter den første av verdenskrig, stadiet der maskineriet måtte jobbe med maksimal kapasitet og uten avbrudd. Tidligere var arbeidskraften den som utførte nesten 90% av arbeidet, sammenlignet med 10% anslått at de laget de første maskinene.
Industrielt vedlikehold stammer samtidig som maskiner begynte å bli implementert for produksjon av varer og tjenester, på begynnelsen av 1800 -tallet. Som et vanlig kjennetegn for alle utviklingsfaser, presenteres behovet for å gjøre det stadig mer spesialisert.
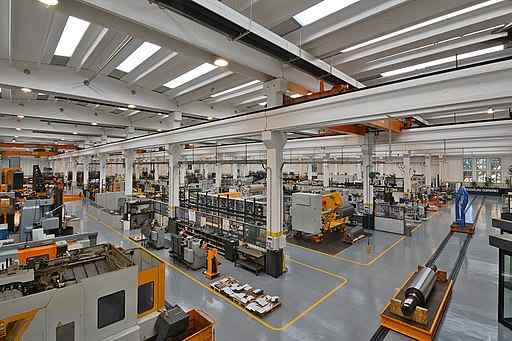
Industrielt vedlikehold er det settet med organisatoriske tekniske tiltak, som tidligere kan utdypes, som tar sikte på å opprettholde utstyrets funksjonalitet og garantere en optimal maskintilstand over tid.
Blant de industrielle vedlikeholdsmålene kan nevnes: bevare maskinens arbeidskapasitet, redusere uforutsette stopp, bidra til økningen i produktivitet, bevare i perfekt stand til produksjonsmidler med en minimumskostnad.
Gjennom industrielle vedlikeholdsplaner er det ment for din levetid.
Industrielle vedlikeholdsoppgaver er ikke eksklusivt for utstyr og maskiner, men for noen fast eller mobil installasjon, industrielle, kommersielle eller spesifikke tjenester, det vil si hvilken som helst type produktiv god.
[TOC]
Stadier fra sin opprinnelse til i dag
Første generasjon: Fra den industrielle revolusjonen til 1950
Det tilsvarer Totalt korrigerende vedlikehold, der noe sammenbrudd forventes å fortsette med den respektive erstatningen. Denne fasen er vanligvis identifisert før 1950 og er den lengste fasen fordi den starter med den industrielle revolusjonen. Vedlikeholdskostnader pleide å være ganske høye og arbeidsledighetstiden for å løse problemene ble forlenget.
Med implementeringen av seriell produksjon, etter første verdenskrig, begynte fabrikkene å etablere minimale produksjonsprogrammer og behovet for å danne et utstyr som konsentrerte seg om å opprettholde maskinene i produksjonslinjene og reduseres til brevet mulig tid stoppet.
Kan tjene deg: Industriell automatiseringParallelt med produksjonsområdet og deretter vedlikeholdet som var fokusert på å reparere korrigerende eller haster feil. I tillegg ble forebyggingsoppgaver tildelt for å unngå feil.
Korrigerende vedlikehold ble preget av ved å presentere høye arbeidskraftskostnader og høye mulighetskostnader, siden tilgjengeligheten av reserve skulle være umiddelbar for å kunne løse eventuelle skader som registrerte.
Blant de mest åpenbare ulempene er kvalitetspåvirkning på grunn av den progressive slitasje av utstyret, risikoen for ikke å ha erstatningstilgjengeligheten, noe som betydde store kostnader, tider drept av plutselige feil og risiko for at andre problemer kunne genereres parallelt.
Andre generasjon: Fra 1950 til 1970
Forebyggende vedlikeholdsarbeid var allerede systematisert for bruk av andre verdenskrig. Og noen år senere dukket det amerikanske kvalitetskontrollsamfunnet frem, noe som bidro til å utføre den statistiske studien av arbeid, og også forbedre kvaliteten på de oppnådde produktene.
Andre generasjon fokuserer på Forebyggende vedlikehold av sammenbrudd, så sykliske og repeterende verk blir utført med en viss frekvens for å oppnå nevnte mål. Denne fasen strekker seg til slutten av 70 -tallet.
I den begynner forebyggende substitusjoner å bli gjort, ettersom forholdet mellom levetiden til utstyret og deres sannsynlighet for svikt blir oppdaget.
Forebyggende vedlikehold har flere modaliteter: det kan være en prosess som skal utføres med jevne mellomrom, vanligvis med et tidsintervall på 6 til 12 måneder. Det kan også planlegges i henhold til produsenter eller av standardene som er fastsatt av Engineering.
En annen modalitet kan ha til hensikt å implementere forbedringer i prosessen, og selv om den ikke har en etablert frekvens, er det en redesign å optimalisere prosessen. Endelig er det autonomt vedlikehold, utført av operatøren med enkle aktiviteter eller rutinen.
Tredje generasjon: Fra 1980 til 1990
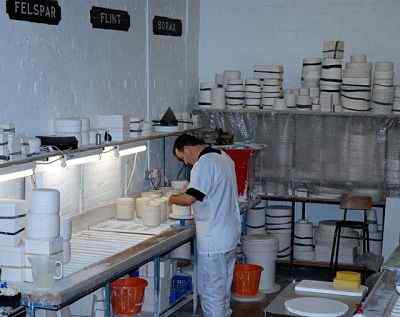
Vedlikehold implementeres på betingelse, det vil si den som avhenger av overvåking av parametere, avhengig av hvilken erstatning eller rekonditionering av maskiner som skal utføres.
Kan tjene deg: telegraf: historie, oppfinnelse, evolusjon, hvordan fungererDette arbeidet er muliggjort takket være tilgjengeligheten av pålitelig inspeksjons- og kontrollutstyr, som gjør det mulig å kjenne utstyrets virkelige tilstand gjennom periodiske målinger.
Det er tiden for Forutsigbar vedlikehold, som besto av tidlig oppdagelse av begynnende symptomer på fremtidige problemer. Studier av årsaks-effekt blir vanligvis utført for å finne ut opprinnelsen til feilene. Et differensierende element på dette stadiet er at de begynner å bli involvert i produksjonsområdene i oppdagelsen av problemer.
En av de store fordelene med prediktivt vedlikehold er muligheten for overvåking og registrering av feil, så det vil være lettere å planlegge fremtidige reparasjoner og mindre intervensjoner av vedlikeholdspersonell vil bli registrert.
Fjerde generasjon: Fra 1990 til i dag
Begynnelsen på denne fasen er vanligvis identifisert på 90 -tallet da amerikanske selskaper allerede hadde innlemmet i dynamikken sin konseptet med total kvalitet som japanske næringer hadde promotert fra 60. Total Quality Management (TQM) forsøkte å skape kvalitetsbevissthet i alle organisasjonens prosesser og menneskene som jobbet med den.
Den fjerde generasjonen tilsvarer Totalt produktivt vedlikehold som er inspirert av den filosofien om japansk opprinnelse som søker dyktighet eller sagt i en setning: Få maksimum med akseptabel kvalitet, i det minste mulig kostnad, i en perle og omfattende forstand. For dette utføres små vedlikeholdsoppgaver som justering, inspeksjon, utskifting av deler og kontinuerlig samhandling med vedlikeholdssjefen.
Programmet fokuserte på den menneskelige faktoren til hele selskapet som forebyggende vedlikeholdsoppgaver er tildelt for å maksimere effektiviteten av varer. Det antar tre prinsipper: hold alltid fasilitetene i god stand, fokus på å øke produktiviteten og involvere helheten i personalet.
Dette er fasen av kontinuerlige forbedringssystemer og er preget av gjennomføringen av handlinger for forbedring og overvåking av handlinger. Vedlikehold blir en fordel, snarere enn et nødvendig onde, og antas som en forpliktelse fra alle avdelinger i organisasjonen.
Målet er å oppnå den totale effektiviteten av utstyret som innebærer økonomisk effektivitet gjennom tilgjengelighet, maksimal ytelse og kvalitetsprodukter.
Det kan tjene deg: Menneskemaskinsystem: Kjennetegn og eksemplerI tillegg implementeres tre andre verktøy vanligvis: risikoteknikk som innebærer å bestemme konsekvenser av feil som er akseptable eller ikke; Pålitelighetsanalysen som refererer til å identifisere gjennomførbare og lønnsomme forebyggende oppgaver; Forbedringen av vedlikeholdbarheten som består i å redusere tidspunktene og vedlikeholdskostnadene.
På dette stadiet har det vært viktige endringer i lovgivningen om sikkerhet og hygiene på jobb, samt mer vennlige praksis for miljøet. Derfor begynte rensende enheter, ekstraksjonsanlegg, støydemping, deteksjonsutstyr, kontroll og alarmer å bli implementert.
I dag anslår eksperter på feltet at vedlikeholdskostnader vil lide en progressiv økning som vil føre til at næringer genererer mer pålitelige og enkle vedlikeholdsprodukter.
Viktigheten av vedlikehold
Industrielt vedlikehold gikk fra å være et nødvendig onde som flere avdelinger i en organisasjon er begått og involvert. Dette er i utgangspunktet fordi den sanne viktigheten av effektiv styring av feil eller problemer med utstyr og fasiliteter har blitt anerkjent, noe som kan påvirke noen av stadiene i produksjonen av varer eller tjenester.
Det skal bemerkes at viktigheten av industrielt vedlikehold ligger i følgende:
- Forhindrer arbeidsulykker og øker sikkerheten for mennesker.
- Reduserer tap på grunn av produksjonsstopp.
- Alvorlighetsgraden av feilene som ikke unngås reduseres.
- Forhindrer skader som kan være uopprettelig i utstyr eller fasiliteter.
- Garanterer akseptabel ytelse av utstyret.
- Lar å dokumentere de nødvendige vedlikeholdsprosessene for hver maskin.
- Forlenger levetiden til utstyr eller varer.
- Beholder produktive varer i trygge og forhåndsopprettede driftsforhold.
- Forbedrer kvaliteten på aktiviteten.
- Tillater riktig utarbeidelse av budsjettet, justert til selskapets behov.
Referanser
- Muñoz Abella, m. (2003) Industrielt vedlikehold. Madrid: Carlos III University of Madrid. Mekanisk ingeniørområde.
- Mora Gutiérrez, a. (2009). Vedlikehold: Planlegging, utførelse og kontroll. Mexico: Alfaomega Grupo Editor.
- Industrielt vedlikehold. (s.F.). Gjenopprettet fra Ecured.Cu
- Barnebarn. Historie med vedlikehold. (2009, 27. mai). Hentet fra industrielt vedlikehold2009.Blogspot
- Villada, "Vedlikehold som en konkurransedyktig strategi", Rev. Fac. Ing. Univ. Antioquia, nei. 17, s. 7-13, 1998.
- Evolusjonen av industrielt vedlikehold: Blogg: ATS. (2019, 26. juli). Gjenopprettet fra AdvancedTech.com
- « Natriumnitrat (nano3) struktur, egenskaper, bruksområder, risikoer
- Euclidian Distance Concept, Formula, Beregning, eksempel »